1. 1.
Deposición química en fase vapor (CVD): Los gases fuente de carbono que se suelen utilizar incluyen hidrocarburos como el etileno y el metano, mientras que para el catalizador se suelen elegir catalizadores metálicos como el hierro, el níquel, el cobalto, etc. El sustrato que se va a depositar (por ejemplo, oblea de silicio, oblea de vidrio, etc.) se coloca en una cámara de reacción para garantizar que la superficie del sustrato esté limpia y plana. La cámara de reacción se calienta a una temperatura adecuada y después se extrae a un determinado nivel de vacío para garantizar la pureza y estabilidad de los gases durante el proceso de reacción. El gas fuente de carbono y el gas catalizador se introducen en la cámara de reacción a través de un sistema de suministro de gas para controlar el caudal de gas y el volumen de flujo. El gas fuente de carbono se disocia en la superficie del catalizador para generar átomos de carbono, que posteriormente se depositan en la superficie del sustrato para formar nanotubos de carbono. Se controla el tiempo de crecimiento de los nanotubos de carbono, que suele oscilar entre minutos y horas, para controlar la longitud y la densidad de los nanotubos. Un crecimiento prolongado da lugar a nanotubos de carbono más largos y densos. Al final del crecimiento, se interrumpe el suministro de fuente de carbono y gas catalizador y la cámara de reacción se enfría a temperatura ambiente. Al final de la reacción, se elimina el gas residual de la cámara de reacción suministrando un gas inerte como nitrógeno o argón.
2. 2. Método de recubrimiento: La suspensión de nanotubos de carbono se recubre sobre la superficie del sustrato por centrifugación, pulverización, cepillado o laminación. Durante el proceso de recubrimiento, pueden controlarse parámetros como la velocidad de recubrimiento y la velocidad de rotación del cabezal de recubrimiento para controlar el grosor y la uniformidad de la película. Tras el recubrimiento, éste se coloca en una zona ventilada o en un banco calentado para inducir la evaporación del disolvente. Una vez que el disolvente se ha evaporado por completo, se procede al secado para formar una película uniforme de nanotubos de carbono. Opcionalmente, la película de nanotubos de carbono se trata térmicamente para mejorar la cristalinidad y las propiedades mecánicas de la película. Las condiciones del tratamiento térmico pueden ajustarse según sea necesario y suelen realizarse bajo una atmósfera de gas inerte.
3. 3. Filtración: Los materiales de las membranas de filtración utilizados habitualmente incluyen membranas de policarbonato (PC), poliéster (PET) y poliamida (Nylon), mientras que el tamaño de los poros suele seleccionarse en función del espesor de la película y la permeabilidad deseados. La suspensión de nanotubos de carbono se filtra sobre la membrana filtrante mediante vacío o presión. Las operaciones de filtración pueden realizarse utilizando equipos como embudos de filtración al vacío o filtros de membrana.
4. 4. Método de despojamiento: los métodos de despojamiento habituales incluyen el despojamiento mecánico, en el que la película de nanotubos de carbono se desprende directamente del sustrato utilizando herramientas de despojamiento (por ejemplo, cintas, rascadores, etc.), cintas, raspadores, etc.); el decapado químico, en el que la película de nanotubos de carbono cultivada se coloca en un disolvente o solución adecuados de modo que se dañe la unión entre la película y el sustrato para realizar el decapado; y el decapado térmico, en el que el sustrato o la película se calientan para expandirlos o contraerlos térmicamente con el fin de destruir la unión entre el sustrato y la película para realizar el decapado. y la película calentando el sustrato o la película, haciendo que se expanda y contraiga térmicamente, rompiendo así la unión entre el sustrato y la película.
5.3.3 Caso práctico: Membranas de ósmosis inversa mejoradas con nanotubos de carbono
Una aplicación única de los nanotubos de carbono, además de las aplicaciones funcionales similares a otros tipos de membranas de filtración, son las membranas de ósmosis inversa. Esta tecnología de separación por membranas es capaz de separar impurezas, iones, microorganismos, etc. del agua, lo que se utiliza ampliamente en los campos del agua potable, el tratamiento de aguas residuales industriales y la desalinización del agua de mar. Sin embargo, la membrana de ósmosis inversa tiene el problema del bajo flujo y la baja eficiencia de procesamiento. Para resolver este problema, los estudiosos introdujeron nanotubos de carbono en las membranas de ósmosis inversa. Los nanotubos de carbono tienen excelentes propiedades, como una elevada superficie específica, alta resistencia, alta conductividad, etc., que pueden formar una especie de canal conductor de protones en la membrana de ósmosis inversa y aumentar el flujo. Al mismo tiempo, los nanotubos de carbono también pueden adsorber iones, microorganismos y otras impurezas del agua, lo que puede mejorar eficazmente la eficacia de la purificación del agua y la vida útil de la membrana de ósmosis inversa. En la actualidad, la membrana de ósmosis inversa basada en nanotubos de carbono se ha puesto en uso comercial, en el campo del agua potable, desalinización de agua de mar, y otras áreas para obtener resultados significativos. En el futuro, la tecnología de investigación y preparación de materiales de nanotubos de carbono se desarrollará aún más, y el flujo y la eficiencia de procesamiento de membranas de ósmosis inversa se mejorará continuamente.
Tabla 2 Comparación de las propiedades de los nanotubos de TiO2, GO y CNT
Propiedades
|
Membranas de nanotubos de dióxido de titanio (TiO2)
|
Membranas de óxido de grafeno (GO)
|
Membrana de nanotubos de carbono (CNT)
|
Estructura del material
|
Nanotubos de óxido de titanio
|
Óxido de grafeno con grupos funcionales que contienen oxígeno
|
Nanotubos de carbono
|
Método de preparación
|
Método de solución Método de deposición de vapor Método electroquímico
|
Método de recubrimiento Método de deposición química de vapor Método hidrotérmico
|
Método de recubrimiento Método de filtración
|
Campos de aplicación
|
Fotocatálisis Dispositivos fotovoltaicos Purificación del agua y del aire
|
Tratamiento del agua Purificación del aire Separación molecular Biomedicina
|
Tratamiento del agua Membranas de ósmosis inversa Separación molecular Biomedicina
|
Ventajas
|
Alta superficie Propiedades fotovoltaicas especiales Actividad fotocatalítica
|
Muchos grupos funcionales que contienen oxígeno Alta actividad superficial Selectividad molecular
|
Elevada resistencia Elevada conductividad Elevada superficie específica Rendimiento ajustable
|
Inconvenientes
|
Proceso de preparación complejo y coste elevado
|
Propenso a defectos estructurales y poca estabilidad durante el proceso de preparación
|
Proceso de preparación complejo Altos requisitos de control del proceso
|
Aplicaciones
|
Tratamiento fotocatalítico del agua Purificación del aire Preparación de dispositivos fotovoltaicos
|
Tratamiento del agua Separación molecular Aplicaciones biomédicas
|
Membranas de ósmosis inversa Separación molecular Aplicaciones biomédicas
|
6 Membranas basadas en marcos orgánicos metálicos (MOF)
6.1 ¿Qué son las membranas MOF?
El
marco orgánico metálico (MOF) es un polímero de coordinación formado por el autoensamblaje de ligandos orgánicos polidentados que contienen oxígeno, nitrógeno, etc. con iones de metales de transición. Consiste en centros metálicos inorgánicos y ligandos orgánicos puente conectados mediante autoensamblaje para formar un material poroso cristalino con una estructura de red periódica. Como material híbrido orgánico-inorgánico, el MOF tiene tanto la rigidez de los materiales inorgánicos como la flexibilidad de los materiales orgánicos.
Las estructuras de tipo backbone en diferentes dimensiones vienen determinadas principalmente por la coordinación entre los ligandos orgánicos y los iones metálicos, así como por los enlaces de hidrógeno. Durante el proceso de síntesis, los reactivos residuales y las pequeñas moléculas de disolventes ocupan los poros de la estructura esquelética, mientras que la eliminación de las pequeñas moléculas por tratamiento de activación puede dejar una estructura de poros persistente. El tamaño y la estructura de los poros pueden modificarse cambiando la estructura de los ligandos orgánicos y el tipo de iones metálicos en la materia prima sintetizada para controlar el área superficial específica y la porosidad para adaptarse a diferentes aplicaciones. En la actualidad, los materiales de esqueleto metalorgánico utilizados junto con ligandos neutros orgánicos heterocíclicos que contienen nitrógeno o con ligandos aniónicos orgánicos que contienen carboxilo pueden sintetizarse en grandes cantidades, lo que presenta un gran potencial de desarrollo y aplicación en la investigación de materiales modernos.
6.2 Cómo producir membranas MOF
1. Método de síntesis in situ: de acuerdo con las propiedades superficiales especiales del propio soporte, éste se introduce directamente en el sistema de síntesis y, en determinadas condiciones, la superficie del soporte y la noche formadora de la película entran directamente en contacto y reaccionan, para preparar una membrana continua. El método de síntesis in-situ es simple y fácil de operar, fácil de realizar la producción a gran escala, pero es difícil preparar membrana MOF continua, porque las propiedades químicas entre los materiales MOF y los portadores son más diferentes, la tasa de nucleación de cristales se reduce, lo que resulta en baja densidad de nucleación heterogénea de cristales MOF en la superficie del portador, y pobre unión entre la membrana y el portador.
2. Método de crecimiento secundario de la semilla de cristal: primero se utiliza el método hidrotérmico para hacer crecer la semilla de cristal sobre el sustrato, y después del proceso de nucleación de cristales, el crecimiento de la capa de membrana, el crecimiento secundario del material para obtener una membrana densa. Por último, las especies de cristal de la superficie porosa del sustrato después de alta temperatura, la reacción de condensación entre los grupos, y los granos de zeolita combinados para formar enlaces covalentes. Sin embargo, el método es algo limitado porque la membrana del filtro no resiste altas temperaturas.
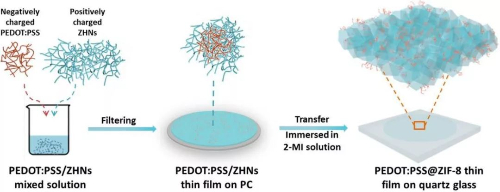
Fig. 10 Síntesis esquemática de una película MOF: Película de PSS@ZIF-8
6.3 Aplicación especializada en la eliminación de metales pesados
Además de las aplicaciones funcionales similares a otros tipos de membranas de filtración, las membranas MOF pueden aplicarse al tratamiento de iones de metales pesados. Las membranas MOF tienen una estructura porosa altamente ordenada formada por iones metálicos y ligandos orgánicos a través de enlaces químicos ligandos. Esta estructura porosa tiene un diámetro de poro y un tamaño de poro sintonizables, proporcionando muchos sitios y canales de adsorción, que son favorables para la adsorción e incrustación de iones de metales pesados. Esto permite utilizar las películas MOF en el campo del tratamiento de aguas, como la eliminación de contaminantes iónicos de metales pesados, como plomo, cadmio y mercurio, de aguas subterráneas, aguas residuales industriales y aguas residuales municipales. Los tamaños de poro altamente controlables y la funcionalización de la superficie de las películas MOF permiten la adsorción eficiente y la separación selectiva de iones específicos de metales pesados. También desempeñan un papel en el tratamiento de adsorción y recuperación para la remediación medioambiental y los procesos de tratamiento de aguas residuales. Las películas MOF pueden capturar y recuperar eficazmente los metales objetivo durante la adsorción de iones de metales pesados. A través de métodos de post-tratamiento adecuados, los iones de metales pesados adsorbidos pueden ser desorbidos de la película MOF, realizando la recuperación efectiva y la reutilización de los recursos metálicos.
7 Membrana filtrante compuesta
Las membranas filtrantes compuestas se diferencian de las membranas filtrantes tradicionales de un solo material en que combinan dos o más materiales para aprovechar al máximo sus respectivos puntos fuertes y compensar las deficiencias de cada uno, logrando así una filtración más eficaz y fiable. Estos materiales pueden ser polímeros, cerámicas, metales, nanomateriales, etc. Cada material tiene unas propiedades físicas, químicas y mecánicas únicas y puede combinarse de forma flexible según los distintos requisitos de filtración.
En las baterías de iones de litio, una membrana compuesta de PVDF-MOF con una capa continua de MOF sirve como diafragma de alto rendimiento. La estructura uniforme de los poros y los canales subnanométricos con sitios metálicos abiertos conectados en la capa continua de MOF pueden generar un flujo de Li+ distribuido uniformemente, inhibir la formación de protuberancias dendríticas y mejorar el rendimiento electroquímico.
Fig. 11 Separador compuesto de PVDF-MOF con capa continua de MOF [5]
En el campo de la desalinización de agua de mar, la destilación por membranas (DM) ha surgido como una estrategia alternativa de desalinización de agua de mar que puede reducir en gran medida los costes de capital y el consumo de energía. En el proceso de DM, se elimina casi el 100% de los componentes no volátiles y no hay limitación en la concentración del agua de alimentación, mientras que el proceso de ósmosis inversa (OI) impulsado por presión tiene menos potencial para tratar soluciones de alta salinidad con baja recuperación de agua. Los componentes volátiles se separan de la mezcla de alimentación utilizando una membrana hidrófoba microporosa, y el sistema funciona por debajo del punto de ebullición del líquido de alimentación. Para las aplicaciones de MD, a menudo se prefieren materiales poliméricos con baja energía superficial, alta estabilidad térmica, estabilidad química e inercia. El politetrafluoroetileno (PTFE) y el fluoruro de polivinilideno (PVDF) se consideran los principales materiales de membrana disponibles en el mercado para la destilación por membrana al vacío (VMD) debido a su elevada estabilidad térmica e hidrofobicidad. El PVDF y el PTFE son los polímeros óptimos para las aplicaciones de VMD debido a su excelente resistencia química y durabilidad. Estas propiedades permiten al PVDF soportar los entornos químicos agresivos que suelen encontrarse en los sistemas VMD, garantizando una fiabilidad operativa a largo plazo. El PTFE, por su parte, desempeña un papel clave por sus propiedades antiadherentes y su excelente resistencia a las altas temperaturas. En VMD, el PTFE ayuda a mejorar el rendimiento de la membrana y evita eficazmente el ensuciamiento, garantizando así un transporte de vapor eficaz y sin obstrucciones a través de la membrana durante la destilación. En las aplicaciones VMD, el uso sinérgico de PVDF y PTFE mejora la durabilidad, la resistencia química y la eficacia operativa del sistema de membranas en su conjunto.
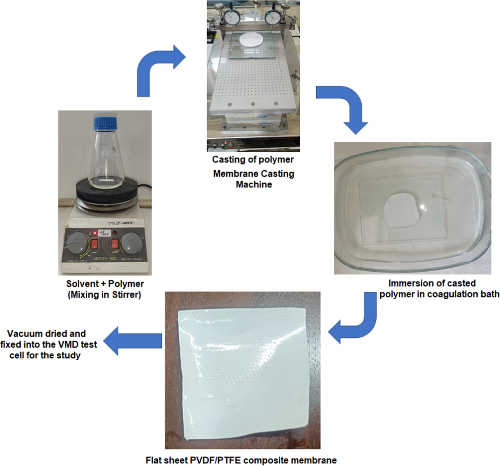
Fig. 12 Diagrama de flujo de la preparación de la membrana compuesta microporosa de PVDF-PTFE [6].
8 Conclusión
Las membranas filtrantes de diferentes materiales se utilizan en diferentes campos debido a sus diferentes características y pueden seleccionarse según diferentes necesidades además del proceso básico de filtración. Las membranas de PVDF pueden utilizarse para filtrar microorganismos como bacterias, y también para la purificación de materiales en la producción química; las membranas cerámicas se utilizan sobre todo en la industria alimentaria para la separación de bebidas alcohólicas; las membranas de nanotubos de dióxido de titanio pueden utilizarse para aplicaciones relacionadas y el tratamiento de iones de metales pesados gracias a sus propiedades fotocatalíticas; las membranas de óxido de grafeno pueden utilizarse para la separación molecular, así como para la desalinización del agua de mar y la separación de petróleo y agua; los nanotubos de carbono pueden utilizarse como membranas de ósmosis inversa; y las membranas MOF pueden utilizarse para separar selectivamente iones de metales pesados debido a la naturaleza de los compuestos de coordinación. Además, según las necesidades de los distintos escenarios de aplicación, se pueden utilizar distintos tipos de membranas de filtración conjuntamente, y el tipo de membrana compuesta puede conseguir un mejor efecto de filtración complementando las características de los distintos tipos de membranas de filtración de materiales.
Stanford Advanced Materials (SAM) no sólo puede ofrecer una amplia gama de productos de membranas de filtración, sino también proporcionar asesoramiento profesional para la selección, que puede
consultar inmediatamente.
Lectura relacionada:
Referencias:
[1] Khayet M ,Feng C ,Khulbe K , et al. Preparación y caracterización de membranas de fibra hueca de fluoruro de polivinilideno para ultrafiltración[J]. Polymer,2002,43(14).
[2] Li M ,Cheng S ,Zhang J , et al. Membranas compuestas a base de fluoruro de polivinilideno con capa continua de marco metalorgánico para separadores de alto rendimiento de baterías de iones de litio[J]. Revista de Ingeniería Química, 2024, 487.
[3] Hu W ,Zhang F ,Tan X , et al. Antibacterial PVDF Coral-Like Hierarchical Structure Composite Film Fabrication for Self-Cleaning and Radiative Cooling Effect[J]. ACS applied materials & interfaces, 2024.
[4. Wei Y ,Li K ,Li P , et al. Enhanced ceramic membranes filtration by PS pre-Oxidation with CuO assisted FeSO4 catalytic for NOM removal in drinking water treatment[J]. Separation and Purification Technology,2024,345.
[5] Ceramic membranes and their application in food and beverage processing[J]. Filtración y separación,2000,37(3).
[6] Mala M ,S. S ,S. F , et al. Sea and brackish water desalination through a novel PVDF-PTFE composite hydrophobic membrane by vacuum membrane distillation[J]. Discover Chemical Engineering,2024,4(1).